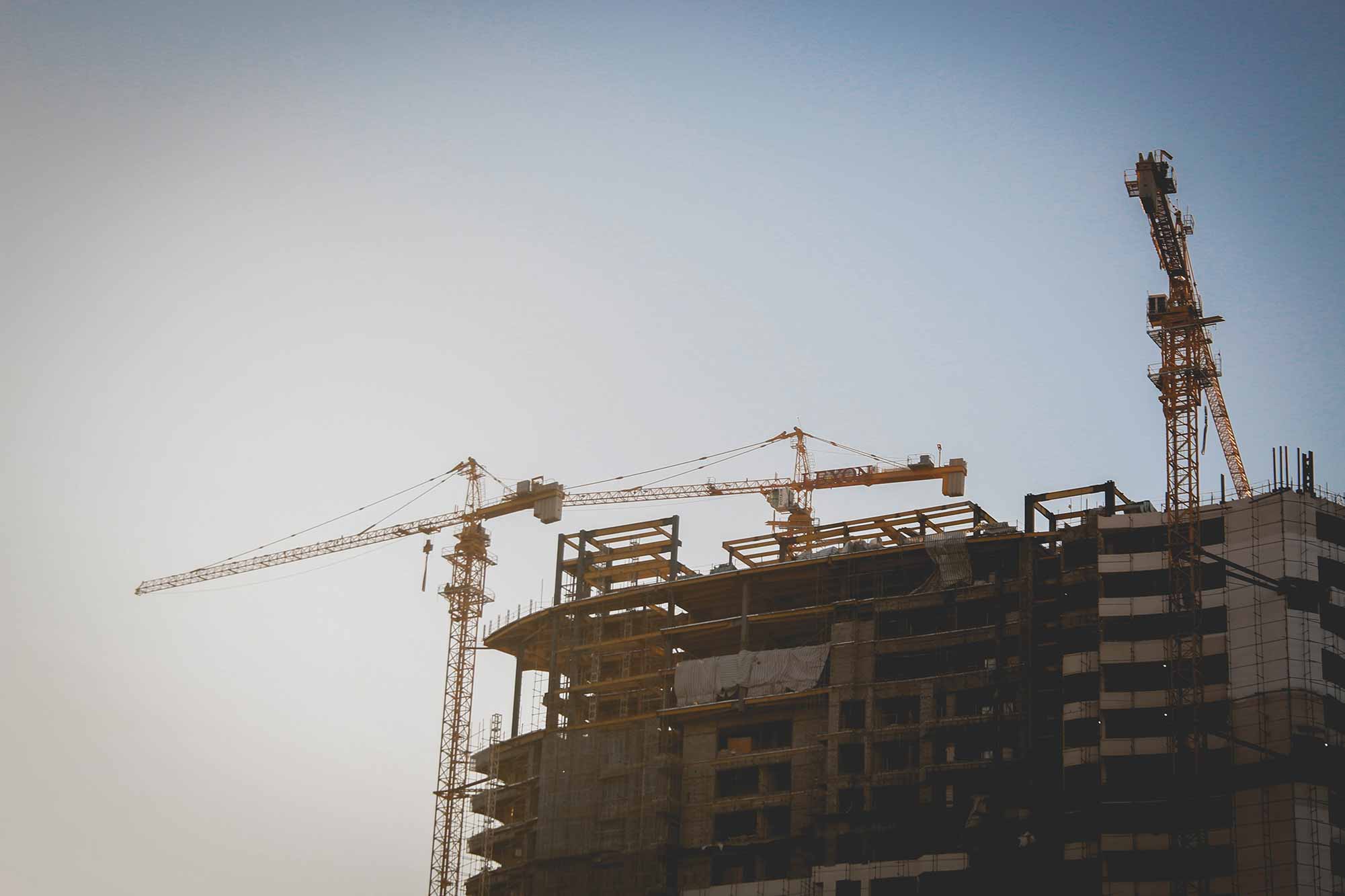
In April 2019, WorkCover Queensland (WCQ) published a new rope access and fall arrest guide to address industry confusion around appropriate safety standards when conducting maintenance on high-rise buildings.
The guide provides an overview of the different types of post-installed anchors, as well as the safe installation and use of anchors and attachment points for building maintenance.
Additionally, it makes reference to relevant Australian and New Zealand workplace health and safety (WHS) standards.
Given that falls are a major cause of death and serious injury in Australian workplaces, the new guide is critical reading for anyone working at heights using rope access or fall arrest systems.
Post-installed anchor points:
The two relevant Australian/New Zealand Standards for fall arrest and rope access systems, AS/NZS 1891.4-2009 and AS/NZS 4488.2-1997 respectively, describe post-installed anchors as “drilled-in, friction or glued-in”.
The WCQ guide suggests that these terms are intended to describe screw bolts, torque-controlled post-installed mechanical anchors assembled with expansion sleeves, deformation-controlled anchors (drop-in anchors) and chemical anchors.
However, despite the Standards apparently referring to these different types of anchor points, the guide does not recommend using all of them for fall arrest and rope access applications.
In fact, it only recommends chemical anchors and torque-controlled thick sleeve expansion anchors for use in these scenarios, and classifies screw bolts, sleeve anchors, coil bolts and drop-in anchors as inadequate for safety applications.
While it is noted that the Standards themselves do not make reference to undercut anchors, the guide approves them for use in fall arrest and rope access systems.
Installation:
Ensuring that anchor points are correctly installed and safely accessible to the user without risk of falling is critical for their effectiveness.
Elemental exposure, thickness and strength of the concrete, and edge and spacing distances all affect the location, choice and strength of the anchor.
Post-installed anchors must also not be loaded in direct tension (i.e. straight pull-out angle), according to the Standards, and the applied shear load should be at least twice the tension load, translating to a maximum pull angle of 20 degrees.
Because of all these factors, an engineering certification and competent installer should be sought out when establishing fall arrest and rope access systems.
In particular, if components from different manufacturers are being used in the same system, further engineering certifications should be sought to verify that the design parameters of the products are not adversely affected.
Additionally, where anchors are being used in direct tension in a multiple attachment point system, an on-site engineering assessment of the concrete substrate must be carried out and documented.
Choosing an installer:
The guide notes that engineering certification of fall arrest and rope access systems appears to be largely carried out remotely, based on the anchor manufacturer’s data.
This has resulted in a large variation of skill levels amongst people installing post-installed anchors, leading to the creation of an anchor installers course by the Australian Engineered Fasteners and Anchors Council (AEFAC).
People who successfully complete the course become certified and are issued a licence. To maintain their competency, they must complete refresher courses every three to five years.
An alternative option to the AEFAC licence is for installers to complete a manufacturer’s installation training course.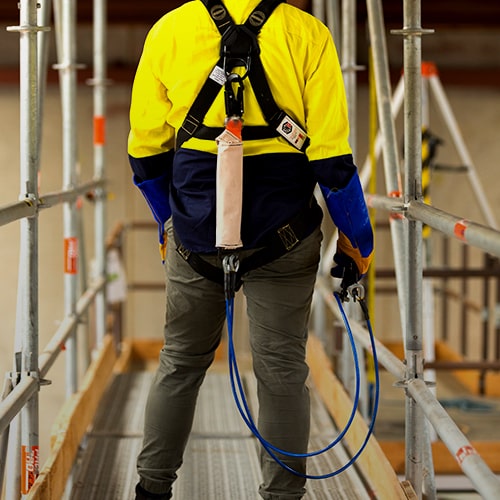
In some situations, depending on the scale and value of the buildings being considered for the installation of anchor points, a Queensland Building and Construction Commission licence is also required.
Regardless of how it is verified, for the protection of workers, it is necessary to ensure that engineering certification is carried out and anchor installers are competent.
Testing and maintenance:
According to the guide, annual proof testing of post-installed anchor points must be performed at least every 12 months by a competent person using manufacturer-approved equipment.
The anchor points must pass a pull-out test with a load equivalent to 50 per cent of their design load.
A visual assessment of the condition of the anchorage system, including the anchor and surrounding concrete, should also be conducted as other factors such as corrosion, concrete damage and anchor movement can affect the integrity and capacity of the system.
Documentation:
On-site documentation of anchor systems should include:
- the location of each attachment point and its intended function
- the name, signature, certification date and company of the certifying engineer
- the name, qualifications and company of the installer
- the name, date and signature of the person carrying out annual inspections
- safe use instructions of the system, including photos and diagrams of attachment points
If documentation of the design, installation and regular testing of the anchors is unavailable, then the fall arrest or rope access system should not be used.
Types of anchor points:
Anchor Point
|
Can it be used in fall arrest/rope access systems?
|
Why / why not / additional information
|
Screw bolts
|
No
|
Difficulties achieving adequate tight tolerances and pull-out resistance when installed in concrete due to reliance on the grooves cut by the bolt’s thread during installation.
Lack of manufacturer information verifying screw bolts for use in safety applications.
|
Torque-controlled thick sleeve expansion anchors
|
Yes
|
Can safely withstand cyclic loading for extended periods of time.
Can be used if manufacturer information states that it is suitable for use in fall arrest/rope access systems.
|
Sleeve anchors (torque-controlled expansion anchors with thin sleeves)
|
No
|
While similar to the above, they are cheaper and not designed for safety applications.
Can resist initial high loading but their ongoing performance for repeated loading is poor.
|
Chemical anchors
|
Yes
|
Only threaded rods or deformed reinforcing bars should be attached with chemical adhesives.
Follow the restriction specified in the Standards to control the risk of degradation of the chemical bond due to elemental exposure.
|
Coil bolts
|
No
|
While commonly used to ensure stability and wind resistance in scaffolding, they do not possess the high load performance needed for safety applications and non-redundant systems.
Unlikely to be recommended by manufacturers for use in fall arrest/rope access systems.
|
Drop-in anchors (deformation-controlled anchors)
|
No
|
Not to be used for new systems, however if they are already installed and the manufacturer’s instructions approve them for safety applications then continued use is allowed with ongoing monitoring.
Typically used for non-critical or redundant (multiple anchor) systems.
|
Single undercut anchors
|
Yes
|
[No further information in the guide]
|
Multiple undercut anchors on a single anchor plate
|
Yes
|
Only to be used as a diverter attachment point in a rope access system.
Minimum spacing distances between anchor points should comply with the manufacturer’s instructions.
|