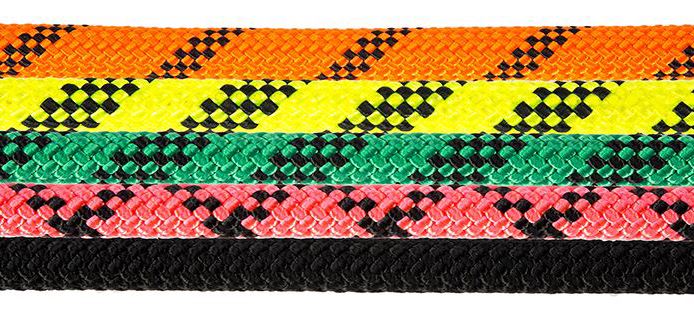
Man-made fibre ropes are used for working at heights and must comply with Australian rope quality standards in their manufacturing and performance characteristics.
While the only visible difference may be colour, height safety ropes are not interchangeable with climbing ropes as they are static instead of dynamic in nature.
“Mountain climbing ropes are elastic, with shock absorbing properties due to the risk of a fall, while static ropes are rigid and will not elongate or ‘bungie’ while in use,” explained Stephen Sugden, LINQ Height Safety Gear’s chief technical officer.
“A window cleaner working on the end of a dynamic rope would bounce up and down like a yo-yo. Using static rope means that workers can hang suspended without any elongation or extension of the rope.”
Static ropes must comply with the Australian Standards AS 4142.1-1993, AS 4142.3-1993, AS 4143.1-1993 and AS 4143.2-1993, which dictate the characteristics, care, safe use and methods of testing of fibre ropes.
Manufacturing characteristics:
While there are no minimum length requirements, static ropes do have prescribed diameters, according to the Australian Standards and there are no set colour requirements.
“Static ropes must be between 11mm and 16mm in diameter, with a five per cent tolerance either side,” said Sugden.
“Additionally, there are length per unit mass requirements, with an 11mm diameter rope requiring at least 10.5 metres per kilogram.”
The diameter of a static rope must be stated on an internal tape (the internal tickertape must be at least 3mm wide) along with the name, trade name or trademark of the manufacturer and the words “for static life rescue lines”.
There must also be a statement of compliance with AS 4142.3 on the external packaging of the rope, which manufacturers must ensure is verifiable - in that the manufacturer must be able to prove compliance to the standard, if called upon so to do.
Strength:
“An important performance characteristic of a static rope is its strength, which is measured with two methods,” said Sugden.
“Firstly, an overhand single knot is made and then the rope is exposed to a force of at least 14.7 kilonewtons (kN). The rope must hold for three minutes without fracturing.”
“The second method is a test of ultimate strength, which should exceed 29.4kN.”
He added that while fall factor was not relevant, static ropes must have a breaking force equivalent to a rope supporting a load of 375kg, using a safety factor of eight.
In other words, the force - in kN - needed to break the rope must be eight times that of the rope strength required to support a static load of 375kg (8 x 375KG = 3000KG =29.4Kn).
Knotability:
Knotability refers to the flexibility of the rope and is measured by making an overhand knot in the test specimen and inserting a tapered rod through the knot whilst the sample is under a given tension, while measuring the diameter to which the tapered rod can be inserted.
“Initially, the rope is under tension of 98N (10kg ONLY) while a conical test rod is inserted through the knot,” explained Sugden.
“This is then replaced with a tension of 9.8n (1kg only) and the conical test rod is also inserted, without allowing the test rod to exert any pressure on the knot, thus measuring the diameter to which the rod can be inserted into the knot.”
The knotability should not be more than 1.1 when measured according to AS4143.2 and is expressed as a ratio of the maximum diameter of the conical test rod which could pass through the knot, to the nominal diameter of the rope being tested. Two tests are conducted and the average is applied.
Other performance characteristics:
The Australian standards also outline requirements for the impact strength index where the rope must be able to withstand two successive prescribed impacts without breaking, elongation and colourfastness of static fibre ropes.
Impact strength measures the ability of a rope to withstand a sudden applied load without breaking.
Elongation is the extension capacity of the rope under load.
The sheath is the outer layer of a rope, which if not manufactured correctly, can dislodge from core, consequently deforming and bunching, increasing the wear on the rope and the likelihood of it jamming in anchor devices.
The rope’s colourfastness is measured against water, friction and light exposure.
Replacement:
“In Australia, it is accepted practice that working at heights fibre ropes should be replaced within 10 years of the date of manufacture,” said Sugden.
“However, as ropes are often exposed to rough edges and the work and grime of a workplace, this will affect the covering materials and integrity of the rope.”
“All ropes should be inspected before each use and if there’s any evidence of nicks, excessive wear, heat burn or fraying, they should be immediately removed from service and replaced.”
He added that to care for ropes between use, they should be stored in a dry location away from dust and direct sunlight.